Sean Kelly Lubrication Systems for Commercial Vehicles
SEIZED BEARINGS ETC - IS THIS YOUR PROBLEM?
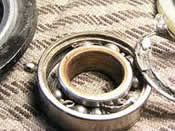
A lack of lubrication is like leaving money on the road. No vehicle owner would contemplate running the engine without oil, yet many bearings are operated without sufficient lubrication. Harsh conditions such as water, dirt, dust, and mechanical loads cumulatively result in high wear rate of bearings, pins, and swivels. Lubrication is therefore absolutely necessary to provide the right lubrication.
THE ANSWER - AUTOMATIC LUBRICATION!
Regular lubrication using an automated and centralised lubrication system is the best solution. While the vehicle or machine is in motion, an automatic lubrication procedure is delivered in time-controlled and metered quantities to all connected points in the system. Lubrication 'in motion' ensure that the lubricant is optimally and evenly distributed within the bearings, thus reducing friction and wear.
The installation of an automatic centralised lubrication system drastically reduces repair and maintenance costs. In addition, lubricant consumption is cut and the life span of wear components is increased. This automatically reduces downtime and operation costs.
In summary, the following advantages are obtained:
THE SOLUTION - THE LINCOLN QUICKLUB® PROGRESSIVE SYSTEM!
Lincoln Quicklub® systems (designed for lubricants up to NLGI Class 2) have been designed to meet the toughest requirements of commercial vehicles, construction machinery, and mining equipment lubrication.
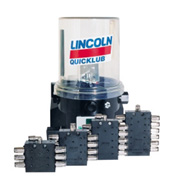
Their operation is based on the reliable progressive principle in which the grease is dispensed by a piston pump via progressive plunger metering devices, without volume losses, to the lubrication points. The lubrication occurs in metered, timed intervals at a maximum pressure of 350 bar. Thus the lubrication of bearings with high-back pressures is also guaranteed.
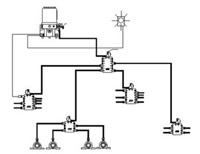
The pump can serve up to three independent circuits, each with its own pump element, consisting of numerous lubrication points with lubricant. Should the question arise of grease or fluid grease, this presents no problem for the Quicklub® system; the high-quality progressive system is designed for all lubricants that range from NLGI 2 downwards.
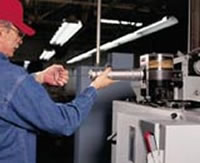
The system is easy to monitor and ensure that the right quantity of grease is supplied to the lubrication points. The pump is simple to fill.
The benefits of the Lincoln Quicklub® System are as follows:
Sean Kelly Lubrication Systems use the Lincoln Quicklub® 203 Pump Versions in their solutions. The features/options of the Lincoln Quicklub® 203 system are as follows:
Sean Kelly Lubrications Ltd Tel: 01242 250802 Mobile: 07778 846528 Fax: 01242 700236 Email: sean.kelly.lube@blueyonder.co.uk or click HERE.